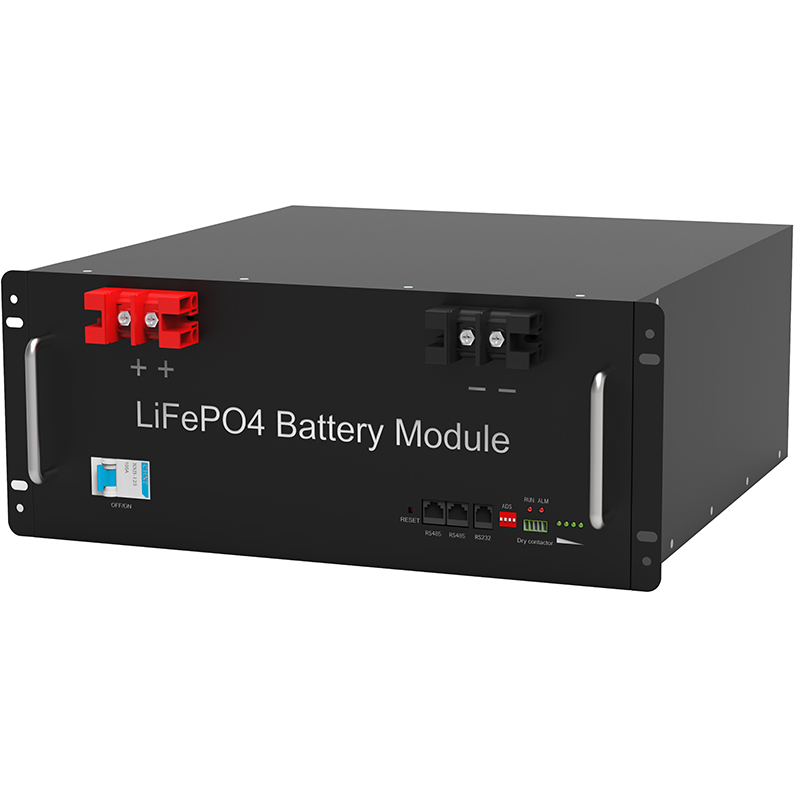
1. The newly installed valve-controlled battery should perform full-capacity check-in charge and discharge, after each 2 to 3 years should be carried out, and the valve-controlled battery after 6 years will be carried out. 1 full-capacity check-in charge and discharge, and the verification of the specific requirements for the specific requirements of the specifically referred to the appendix E1. For substations of only one set of batteries, this set of batteries should be fully capacitated.
2. Regular inspection management of communication uninterruptible power supply devices for scheduling automation systems
3. The battery running time has been discharged from 6 months within 2 years, and the 3 months of 2 years
Electrical test, at least once a depth discharge test (capacity greater than 50%) related to battery pack verification test
Second, the power supply is regularly checked
1. Long-term power supply operation mode or only the operating mode of the battery is not limited, and cannot be judged whether the existing capacity of the battery is lost or dry. Battery capacity defects can only be found by verifying by verifying.
2, the whole station has two sets of batteries or a set of batteries (need to have a standby battery pack), then run, another set of exit operations for full-capacity check-in discharge. Discharge I10 constant current, as a battery voltage dropped to 1.8V or battery pack voltage dropped to 1.8V × N, stop discharge, and time-constant current charging-constant voltage charging-floating charge. If the battery pack has a total of 80 ℅ or more, the battery pack is less than 80 ℅ or more, and the replacement should be arranged.
3. Before the charging test of the battery pack, it should be carefully checked whether all connectors are tightened. In the verification test, the battery discharger and the battery should be fixed to the wire bolt, and it is not connected to the clip to ensure the connection is reliable. The battery temperature measurement is measured and measured using an infrared thermometer during the discharge process and the ambient temperature, the battery unit voltage, a single battery terminal voltage, discharge current, and discharge time. The battery cell voltage should be measured every half hour. The backward battery monomer with a significant decrease in individual voltage decline should also be strengthened, and the number of times of measurement is increased.
Regulations on the nuclear storage unit
Third, the technical specifications of the Substation DC power system
1. After the initial charge is completed, the battery pack should be tested. The newly installed battery pack is less than 100% C10 in the case of sufficient electricity, and the group of batteries should be replaced.
2, initial charging, battery pack capacity test, monomer battery voltage value, internal resistance value, etc. should be long-term preservation as an acceptance information for long-term comparison determination when maintaining the batteries.
Fourth, the requirements for the nuclear storage unit
1. Check the battery pack capacity test
Capability test according to battery nominal capacity: at least once per hour, after 8 hours, at least every half an hour, the monomer battery voltage is released to 1.8V. The discharge instrument should be used for automatic dischargers. Within the three charge and discharge cycles, if the rated capacity value is less than 100%, this set of batteries are unqualified.
2, inspection standards and methods:
Exit operation Perform full capacity check-in discharge. Discharge I10 constant current, as a battery voltage dropped to 1.8V × n, stop discharge, the battery is not activated, and the battery's end voltage satisfies the battery after activation. After the time, I10 current is used for constant current limit charging - constant pressure charging - floating charge. If three full-core pending charges, the battery pack is not more than 80 ℅ above its rated capacity, and the replacement should be arranged.
(Note: 1. In the verification test, the battery discharger and the battery should be fixedly connected with the wire bolt, and it is not connected to the clip to ensure the connection is reliable. 2. Extraction of battery units per hour during the discharge process, single battery end Voltage, discharge current, discharge time for measurement and recording. The last hour should measure the primary battery cell voltage every half hour.)
V. Interpretation of the provisions of the verification test
1. The purpose of the verification test: found that the battery capacity defect.
1.1 Only the battery capacity defect can be found by verifying.
Nuclear Test Calculation Formula: C = IF × T (AH)
Where: C-battery pack capacity, unit: ah (time);
IF-constant discharge current, A (ampere);
T-discharge time, H (hour).
1.2 Generally, discharge current constant current is discharged at 10 hour rate, i10 = C10 / 10.
2. Interpretation of the specification of the verification test
2.1 Cycling test cycle:
New installation, full-capacity verification charge and discharge;
Every 2 to 3 years later, 1 full-capacity check-in charge and discharge should be performed;
After 6 years, it is appropriate to carry out 1 full capacity check-in charge and discharge.
2.2 Test standards and methods of nuclear contraction test:
Discharge I10 constant current;
When either a battery voltage dropped to 1.8V, or when the battery pack voltage drops to 1.8V × N, the discharge is stopped.
Timely use I10 current for constant current limit charging - constant voltage charging - floating charge.
New installation acceptance, within three charge and discharge cycles, if it is less than 100% of the rated capacity value, this group of batteries is unqualified.
It has been shipped, and if it is discharged through three full-core, the battery pack capacity is less than 80 ℅ above its rated capacity, and the replacement should be arranged.
2.3 Data Save of Nuclear Test:
Battery group capacity test, monomer battery voltage value, internal resistance value, etc. should be preserved for a long time as an acceptance material, so that the comparison determination is compared when the battery is maintained.
2.4 Notes of Nuclear Control Test
N before testing, check whether the connecting strip is tightened one by one.
The connection strip between the N battery is loose, and the contact resistance of the looseness will increase.
During the N discharge process, there is a large current, the contact resistance is increased, which will cause continuous heat, and the temperature is increased, and it is a safety hazard of fire accidents. (The temperature is proportional to the square of the current, which is proportional to the size of the contact resistance, which is relatively than the heat dissipation area of the connector.)
n therefore, before the test, all the connectors must be checked one by one.
In the N test, the discharge device and the battery should be secured to the wire bolt, and it is not connected to the clip.
N When connecting with a clip, there will be three resistors: the resistance between the clip and the stainless steel screw, the resistance of the stainless steel screw itself, the stainless steel screw thread and the thread of the battery screw head, resulting in the calibration discharge.
N The increase in contact resistance is a different clamp or crimping method. In different large currents, the root cause of contact point is generated;
The N connection may not be fastened, resulting in an increase in contact resistance. During the discharge process, the connection will increase the temperature, resulting in continuous red heat, and become a safety hazard of fire accidents.
N When using a wire bolt connection, it must be connected.
During the N discharge process, the battery temperature measurement is measured using an infrared thermometer every 1 hour;
N-series discharge battery pack, when discharge, individual backward batteries, the end voltage can be changed;
N u = e-i * r, where u is the end voltage, E is the electric potential, i is the discharge current, and R is the battery internal resistance; cause U is a negative value, E n During the entire discharge process, the battery cell changes in order to be charged, the discharge process changes to the charging process; at the initial, U is large, the reason is that the R is large, E n Temperature, which is beneficial to find these individual backward batteries in time to avoid hidden dangers of fire accidents
During the N discharge, measure with the recording battery pack voltage, a single battery terminal voltage, discharge current, and discharge time every 1 hour.
n The last hour should measure the battery cell voltage every half hour.
Sixth, the instrument for the verification test
It is advisable to use the automatic discharge instrument "automatic", mainly in:
1. Automatically stop discharge according to the set termination conditions. In general, there are four termination conditions: the monomer voltage is less than 1.8V, 2, the whole set voltage is lower than N × 1.8V, the discharge time reaches the set value, and the release capacity reaches the set value;
3. Automatically record the parameters during the discharge process, such as the end voltage of each battery, the end voltage, discharge current, discharge time of the entire set of batteries, and no longer record.
4, automatically generate reports. After the test is completed, a test report is automatically generated according to the requirements.
Article from: http://www.brcpower.com/ Recommend: LiFePO4 Battery Manufacturer Energy storage battery Manufacturer Integrated machine energy storage battery series Manufacturer Lead lithium battery Manufacturer Outdoor Backup Battery Manufacturer Portable outdoor power supply Manufacturer Power battery Manufacturer Powerwall LiFePO4 Battery Manufacturer Battery rack Manufacturers Telecom LiFePO4 Battery Manufacturer Wall mounted battery storage Manufacturer China Lifepo4 Battery