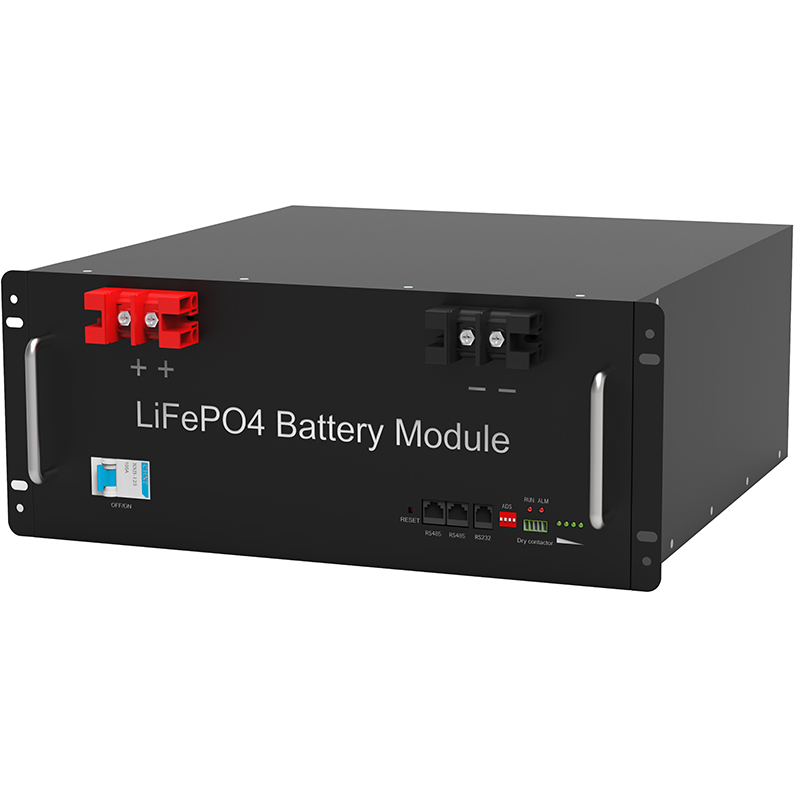
2 overall design ideas
The system block diagram of a large-capacity battery intelligent efficient charging controller is shown in Figure 1, mainly divided into two parts: main circuits and control circuits. Including: power module, charging main circuit module, analog detection module, display, and alarm module, and PWM driver modules [2].
System Working Principle: 380V AC voltage input, transition module and three-phase bridge rectification, DC / DC transform module converts to battery-acceptable charging voltages. The control circuit uses the DSP chip as the main controller, collects parameters such as charging voltage, charging current, temperature, etc. in real time, and converts the AD in the DSP to digital quantities and determines whether overvoltage, overflow, and overheating. If there is a fault, the DSP is turned off immediately and a sound and light alarm is issued. If it is normal, use
The PWM pulse based on the fuzzy self-tuning PID control algorithm generates the corresponding duty cycle to control the DC / DC conversion circuit to perform charging the battery.
3 hardware circuit design
3.1 three-phase full bridge rectifier circuit design
The three-phase full bridge rectifier circuit consists of six diodes and is uncontrollable. The input 380V / 50Hz AC electrically passes through the transformer to obtain a one-way pulse voltage of 24V. The capacitive filter circuit is then used, and the ripple is filtered to obtain a smoother DC signal.
3.2 DC-DC circuit design
In the design, the DC-DC circuit module design is implemented in the design of the BUCK circuit. Inductive current work in continuous mode. The design is 13.4V. In the figure, Q1 is the main power tube, and the IRF640N, C1 and C2 are used primarily to filter out low frequency noise, and C3 is used to filter out high frequency noise [3]. D2 is to prevent the battery from causing the circuit to malfunction between the battery and the charger.
3.3 Drive circuit design
The PWM signal generated by the DSP passes the buffer SN74HCT 244N, and the output amplitude is 3.3V, and the amplitude 12V pulse signal is enlarged after amplifying the amplified circuit, and the input to IR2112 is isolated and enlarged to drive the main power tube Q1 [4]. In the design, the BUCK converter main power tube IRF640N is driven by IR2112 floating channel.
3.4 Temperature detection circuit design
In order to prevent the temperature during charging, the temperature of the battery is monitored in real time on the battery damage. Temperature detection is achieved with a linear digital temperature detection chip DS18B20. In the form of an external power source, only one line is connected to the IO port of the microcontroller, the temperature detection of the battery can be completed.
3.5 Signal Acquisition Conditioning Circuit Design
In order to ensure the system security, stable work, the main control unit is monitored to the charging voltage and charging current of the battery in real time. The monitoring information is then sent to the AD comes with the DSP, and the control signal is obtained by analyzing and calculating. When the system voltage sampling is realized by the resistance division, the capture of the voltage signal is achieved by two-stage op amp, the first stage operational amplifier outputs the voltage signal of -5V ~ 5V; the second arithmetic amplifier output voltage signal is 0 ~ 3V, satisfied DSP's AD input voltage range. [5] is sampled by sampling resistance Rt when the sample of the charging current is sampled. The circuit is shown in Figure 4 below. After the sampling signal is added, a voltage follower is added, and the AD conversion accuracy is increased. The regulator diode in the figure is to prevent damage to the sampling signal voltage above 3.3 V on the DSP.
4 software design
The smart charger uses three-stage pulse charging mode to keep the charging current tightly follow the battery of the battery to avoid the end of the battery charging, and avoid the heat loss caused by excessive current. First initialization, the interrupt initialization, PWM module initialization, and timer initialization are completed. Enter the main program loop, the ADC sampling data monitors the battery charging process in real time, and determines whether constant current charging; if it is not satisfied, it is determined whether to satisfy constant pressure charging; if it meets the incoming constant voltage charging, The charge is satisfied, and it will enter the floating charge [6]. In order to avoid polarization, after the charging is completed in each stage, the battery is discharged to the battery. In real time during the charging process, the battery charging temperature is real-time, and the over temperature is alarm, and the temperature protection control is performed.
Article from: http://www.brcpower.com/ Recommend: LiFePO4 Battery Manufacturer Energy storage battery Manufacturer Integrated machine energy storage battery series Manufacturer Lead lithium battery Manufacturer Outdoor Backup Battery Manufacturer Portable outdoor power supply Manufacturer Power battery Manufacturer Powerwall LiFePO4 Battery Manufacturer Battery rack Manufacturers Telecom LiFePO4 Battery Manufacturer Wall mounted battery storage Manufacturer China Lifepo4 Battery