source:Geerady       date: 2022-06-17
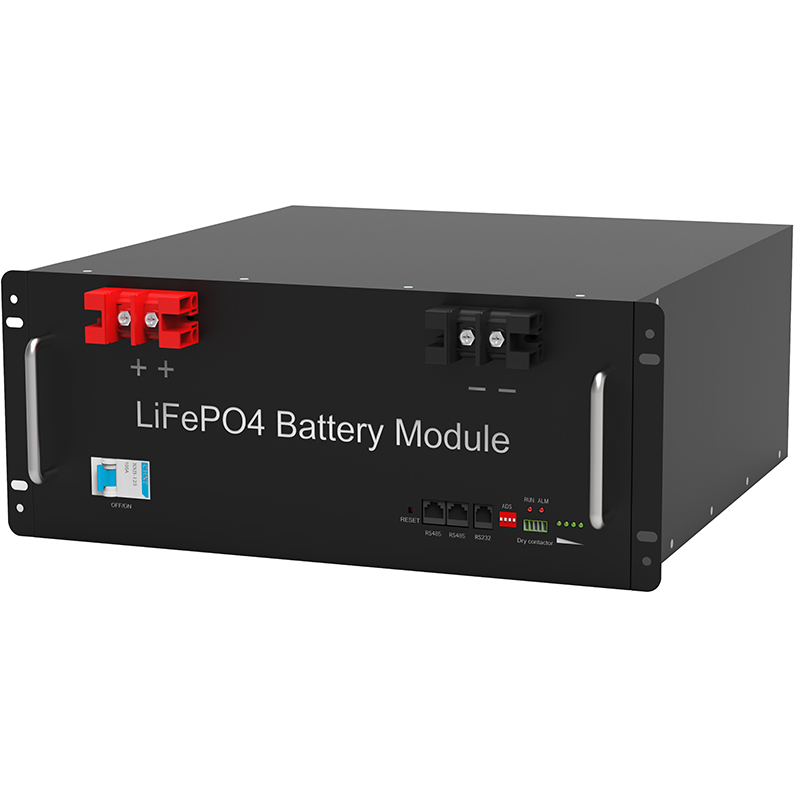
The package is a key step in solar cell production. There is no good packaging process, and how good batteries are also produced in a good components. The battery packaging can not only make the battery life, but also enhance the resistance of the battery. The high quality and high life of the product are the key to win customer satisfaction, so the packaging quality of the component board is very important.
process:
1, battery detection - 2, front welding - test - 3, back side line - test - 4, laying (glass cleaning, material cutting, glass pretreatment, laying) - 5, laminate --6, goen edge ( Defelt, cleaning) - 7, border frame (glue, angular key, punching, frame, rubber) - 8, welding junction box - 9, high pressure test - 10, component test - appearance Inspection - 11, packaging
How to ensure efficient and high-life components:
1, high conversion efficiency, high quality battery block;
2, high quality raw materials, such as: high cross-linking EVA, high-bonded strength package (neutral silicone resin glue), high-profile high-profile temperatures, etc .;
3, reasonable packaging process
4. Work style of employees;
Since the solar cell is a high-tech product, some detailed problems during the production process, some inconspicuous problems should be wearing gloves without wearing, and should be uniformly painted reagents, and the draft is the enemy affecting product quality, so in addition to formulating reasonable Outside the production process, employees are serious and rigorous and very important.
Solar Battery Assembly Process Description:
Process Description: Only simply introduce the role of the process and give you a sense of understanding.
1. Battery test: Due to the randomness of the battery pack, the battery performance produced is not the same, so in order to effectively combine the performance of the battery, the battery should be classified according to its performance parameters; Classify it by testing the output parameter of the battery (current and voltage). To increase the utilization of the battery, make a quality of battery components.
2, front welding: Welding the bus belt on the main grid line of the front (negative electrode) of the battery, the bus belt is a tinned copper strip, we use the welding machine to spot welding tape in the form of a multi-point on-line. The heat source for welding is an infrared lamp (using the thermal effect of infrared). The length of the solder tape is approximately twice the length of the battery side. Many out of the soldering belt is connected to the back electrode of the back of the battery sheet when welded on the back.
3, the back side connection: Back welding is to connect 36 pieces of battery strings together to form a component string. The process we currently use is manual, and the positioning of the battery mainly rely on a membrane table, and there is 36 recesses of the battery.
The slot, the size of the groove corresponds to the size of the battery, the position of the groove is well design, and the components of different specifications use different templates, the operator uses the electric soldering iron and solder wire to weld the front electrode (negative electrode) of the front battery "to" On the back electrode (positive electrode) of the rear battery, 36 sheets are sequentially joined together and the positive and negative electrode welding leads in the component string.
4, laminated laminated: After the back is connected, after passing the test, the component string, glass and cutting EVA, glass fiber, and back plate are laid well according to a certain level, ready to laminate. Glass is coated with a reagent (Primer) in advance to increase the bonding strength of glass and EVA. When laying, ensure the relative position of the material such as the battery and the glass, adjust the distance between the battery, and lay the basis for laminate. (Layer: By downward: glass, EVA, battery, EVA, fiberglass, backplane).
5. Component lamination: Put the laying battery into the laminate, extract the air in the assembly by vacuuming, then heating EVA melts to bond the battery, glass, and backplane together; finally cooling the removal assembly. The lamination process is a key step in component production, and the lamination temperature laminated time is determined according to the nature of EVA. When we use rapid curing EVA, the lamination cycle time is about 25 minutes. The curing temperature is 150 ¡ã C.
6, the trimming: After the EVA is melted, the curved curing is formed outward due to pressure, so it should be removed.
7, frame: Similar to a frame to be fitted with glass; to the glass assembly, increase the strength of the assembly, further seal the battery assembly, extend the battery life. The gap between the border and the glass assembly is filled with silicone resin. The angular keys link between each frame.
8, welding junction box: Welding a box at the back of the component to facilitate the connection between the battery and other devices or batteries.
9, high pressure test: High-pressure test refers to the application of a certain voltage between the component border and the electrode leads, the pressure resistance and insulation strength of the test assembly to ensure that the components are not damaged under harsh natural conditions (lightning strike, etc.).
10. Component Test: The purpose of the test is to calibrate the output power of the battery to test its output characteristics, determine the quality level of the component
Recommend:
LiFePO4 Battery Manufacturer
Energy storage battery Manufacturer
Integrated machine energy storage battery series Manufacturer
Lead lithium battery Manufacturer
Outdoor Backup Battery Manufacturer
Portable outdoor power supply Manufacturer
Power battery Manufacturer
Powerwall LiFePO4 Battery Manufacturer
Battery rack Manufacturers
Telecom LiFePO4 Battery Manufacturer
Wall mounted battery storage Manufacturer
China Lifepo4 Battery
LiFePO4 Battery 48V 150AH
LiFePO4 Battery 48V 100AH