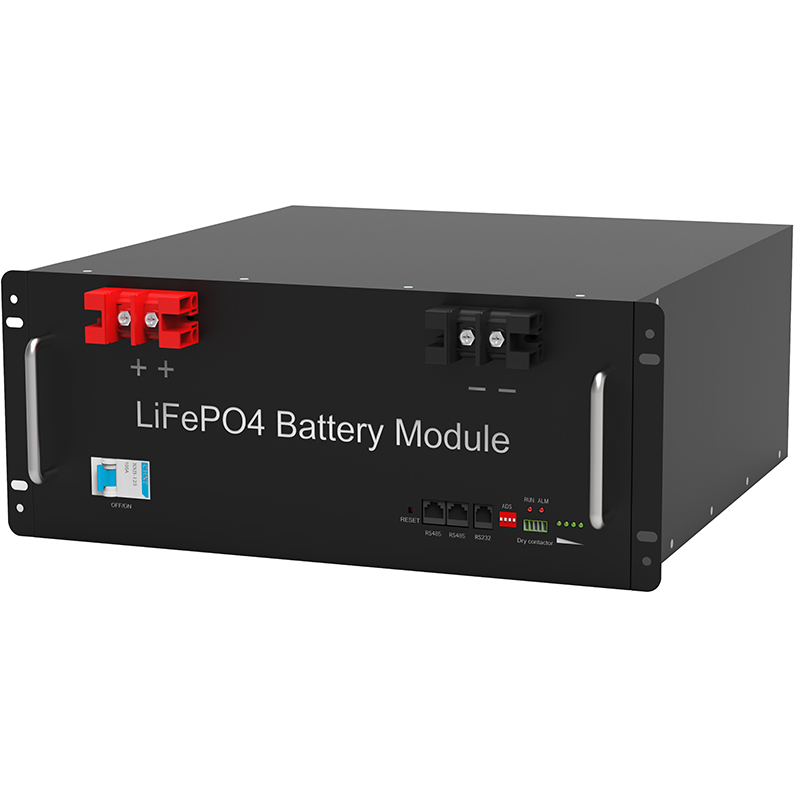
The repair size can be standard and free. When a standard repair size is used, one of the parts (such as the journal) is processed to a given standard size, and the part (such as a bearing sleeve) is prepared in advance according to this standard dimension. This will do not have to match the part. However, this method is more than the metal that needs to be cut more than a method (free size method) that only repairs the axial neck to the correct geometry.
When processing the free repair, the metal cut from the part is small, as long as the part is restored to the normal geometry, but the part is equipped with the part must be formulated at the time, so the service life of the part is extended.
With standard repair size, the parts are interchangeable, which can shorten the repair cycle, and reduce the cost of repair, so it is best to adopt standard repair dimension.
Repair crankshaft, camshaft, cylinders, etc. use standard repair sizes. When preparing standard size parts, the accessories factory can prepare the shaft watt-axis and piston and piston ring in advance according to the specified repairs.
Second, additional part method: When the shape of the complicated part is partially worn or damaged exceeds the allowance, the partial wear or damaged portion of the part is removed, and the size is trimmed, and then add an additional part (compensation part). After adding addition, the original parts are restored to normal shapes and sizes.
This method can be used for vehicles that have been repaired by multiple trucks, buildings, cylinder head, seat, rolling bearing hole, journal, ring gear, etc.
Additional parts are typically made of the same material of the repaired parts. For cast iron parts, the sleeve can be made of 20 steel with a minimum thickness of 2.5, 3 mm, surface roughness, and hardness should comply with technical conditions, and it is necessary to perform heat treatment if necessary. Additional parts should be connected to the base part, and then carry out mechanical processing, so there is a certain processing margin at the time of manufacture.
Third, pressure processing repair: pressure processing repair is to restore the size and shape of the part damage site by plastic deformation of the part.
The pressure processing repair is characterized by high repair quality, provincial and labor, high productivity. Commonly used pressure processing repair methods are: swelling (shrinkage), exclusive, unute, school (positive), etc.
(1) Rough method. Reduce the length of hollow and part of the solid parts to expand its cross-sectional area. This method is used for repair of an emblem coefficient working surface, a journal, and the like.
(2) The elongation method is to shrink the partial cross-sectional area of the part by extending method to restore the length of the tie rod, axis and other parts.
(3) Pressure colony is used to remove the residual deformation of the part on the part by plastic deformation, twisted, warped), and the damaged parts are repaired. When using a pressure colonial direct axis, the bus carrier can be on the V-shaped block, so that the curved arch is loaded, and a certain anti-strand is given, the anti-strand should be 2 to 5 times the amount of bending, and the load Stay 1.5 a 2min.
The part of the pressure-proof movement will often be bent deformation again, in order to stabilize the pressure of the pressure to stabilize, the heat treatment of stable deformation should be performed. Parts to sub-conditioning or normal treatment can be heated to a temperature higher than the recrystallization temperature (450 1 5000c), heat insulation 0.5 2 h; for surface quenching parts (camshaft, crankshaft) can be heated to 20012500C Insulation 5-16h.
When the accuracy of the part is high or the amount of deformation is 0.05% or less of the shaft length of the shaft, a partial surface cold as a deformation method can be repaired. Recommend: LiFePO4 Battery Manufacturer Energy storage battery Manufacturer Integrated machine energy storage battery series Manufacturer Lead lithium battery Manufacturer Outdoor Backup Battery Manufacturer Portable outdoor power supply Manufacturer Power battery Manufacturer Powerwall LiFePO4 Battery Manufacturer Battery rack Manufacturers Telecom LiFePO4 Battery Manufacturer Wall mounted battery storage Manufacturer China Lifepo4 Battery