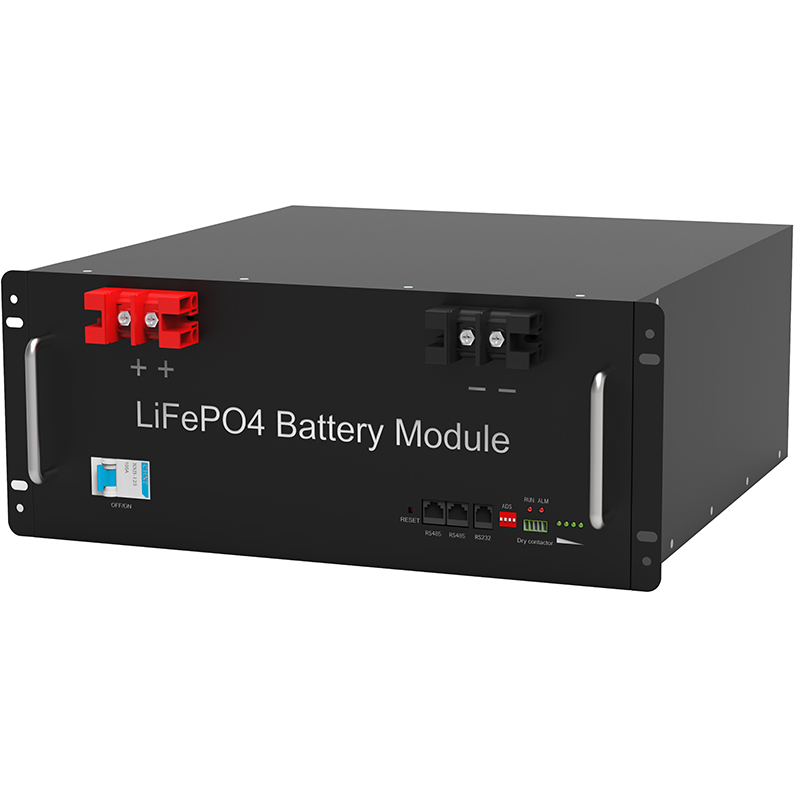
1, electrode and catalyst
The electrode consists of a carrier and a catalyst layer. The catalyst is deposited on the surface of the carrier with chemical adsorption method, and the electrochemical reaction occurs on the catalyst layer. The main components of the catalyst layer include carbon support, highly dispersed platinum catalysts and hydrophobic media such as polytetrafluoroethylene, PTFE. The activity of the platinum catalyst depends on the type of catalyst, grain size and surface area, and the like. The crystal grains is smaller, the greater the specific surface area, the higher the activity of the catalyst.
The structure of the carbon carrier affects the performance and life of the electrode. The main role of the carbon carrier is as follows:
(I) dispersion catalyst;
(2) Provide a large amount of micropores for the electrodes;
(3) Adding conductivity of the catalyst layer.
There are two types of carbon black, namely, acetylene black and furnace carbon black.
2, substrate
As the substrate of the electrode support material, it is adjacent to the catalyst layer, and electrons and reaction gases may be passed. From performance, the electrode substrate should meet the following conditions:
(1) Stability in working conditions and phosphate;
(2) Good conductivity of electricity and heat;
(3) Porous properties to diffuse the reaction gas efficiently;
(4) Good mechanical strength can withstand high pressure operation.
At the operating temperature, 100% phosphoric acid has strong corrosive, graphite is considered to be the preferred material. The production of the substrate is to mix the graphite fibers, the phenol resin with the binder, and then bake at a high temperature.
3, electrolyte
The choice of phosphoric acid is based on the following reasons:
(1) Work at high temperatures;
(2) can be resistant to COT;
(3) low vapor pressure;
(4) High oxygenolysis;
(5) Good ion conductivity at high temperatures;
(6) Low corrosion speed at high temperature;
(7) Large contact angle (greater than 900).
4, matrix
The phosphoric acid is in the matrix, and the function of the substrate is to adsorb the acid in it. Requirements to the matrix include:
(1) There is a good capillary effect on phosphoric acid;
(2) Electrical insulation;
(3) Prevent the cross penetration of the reaction gas in the battery;
(4) Good thermal conductivity;
(5) Stability under high temperature operating conditions;
(6) Sufficient mechanical strength.
In addition to mechanical strength, the current matrix structure can meet other requirements.
5, separator
The effect of the separator is to prevent the bonding in the yin, an anode gas mix, and turn the two electrodes. Gas leaks can result in reduced performance, and even hazardous conditions.
The requirements for the separator are as follows:
(1) sufficient gas tightness to prevent the penetration of the reaction gas;
(2) Chemical properties in high temperature, high pressure and phosphoric acid;
(3) Good conductivity, thermal conductivity;
(4) Sufficient mechanical strength.
6, gas supply system
The gas supply system is a device that supplies two reaction gases to the battery, which is divided into two types, namely internal and external pipeline structures. In the internal pipeline system, the air supply line is composed of a hole perpendicular to the battery plane and penetrating through the battery stack element. External pipelines typically connect the pipe box on the side of the battery stack.
The design principles of the pipeline include:
(1) Small pressure drop as much as possible;
(2) Good insulation;
(3) sufficient chemical stability;
(4) Sufficient mechanical strength;
(5) The welding of the pipeline must be firm under any case (including sudden accident), and has a lower coefficient of thermal expansion.
7, cooling system
There are 3 cooling methods in PAFC: air cooling, insulating liquid cooling and water cooling. From the cooling performance, the water is best, suitable for larger power plants. The air cooling is relatively cold and simple, suitable for relatively small power stations, but relatively more electrical energy circulation cools air, so inevitable reduction in net efficiency. When considering the overall cooling performance and system, indirect liquid (oil) cooling system is between air and water, but it is very compact and is not easy to corrode. Recommend: LiFePO4 Battery Manufacturer Energy storage battery Manufacturer Integrated machine energy storage battery series Manufacturer Lead lithium battery Manufacturer Outdoor Backup Battery Manufacturer Portable outdoor power supply Manufacturer Power battery Manufacturer Powerwall LiFePO4 Battery Manufacturer Battery rack Manufacturers Telecom LiFePO4 Battery Manufacturer Wall mounted battery storage Manufacturer China Lifepo4 Battery